What is NAS in Oil Analysis
NAS stands for “National Aerospace Standard” and is used to describe a system for measuring the cleanliness of fluids, including oils.
In the context of oil analysis, the NAS system is used to determine the level of particulate contamination in the oil, which can be an indicator of wear and damage in machinery. The NAS system assigns a cleanliness code to the oil based on the number and size of particles present per unit volume of fluid.
The NAS code is determined by counting the number of particles in the oil that are larger than a specific size, usually 5, 15, or 25 microns. The total number of particles in each size range is then used to calculate the NAS code, which ranges from 0 to 12.
A lower NAS code indicates cleaner oil with fewer particles, while a higher NAS code indicates more contaminated oil with more particles. The NAS system is commonly used in the aviation and aerospace industries, as well as in other industries that rely on hydraulic systems and lubricated machinery, to monitor the condition of fluids and detect potential issues before they become more serious problems.
Particle Count Analysis (NAS Analyzer)
Understanding NAS Values in Engine Oils
In power plant we are doing particle count analysis by Spectro LNF Q200 which is report given based on standard NAS 1638 and ISO 4406. The National Aerospace Standard (NAS) 1638 was developed in the 1960s to help control the contamination levels of hydraulic fluid within hydraulic components. NAS 1638 became a standard not only for the aerospace industry but also throughout many other industries as well. The latest version of NAS 1638 is SAE 4059.
Nevertheless, in many areas of industry, NAS 1638 has largely been outpaced by the ISO 4406 standard in recent years. Both NAS 1638 and ISO 4406 focus on the methods for calculating particle counts or solid contamination levels within a fluid.
NAS 1638 represents the counts of particles in five size groups:
- 5 to 15 microns per 100 milliliters (mL)
- 15 to 25 microns per 100 mL
- 25 to 50 microns per 100 mL
- 50 to 100 microns per 100 mL
- >100 microns per 100 mL,,
ISO 4406:1999 represents the counts of particles in three size groups:
- >4 microns per 1 mL
- >6 microns per 1 mL
- >14 microns per 1 mL
From these five groups of particle sizes and a basic particle size distribution, NAS 1638 reports the results in 14 distinct classes of particle counts numbered 00, 0 and 1 through 12, with 00 being the cleanest and 12 being the dirtiest. Each proceeding class contains twice the number of particles as the previous class per each of the five particle size groups (see the table below).
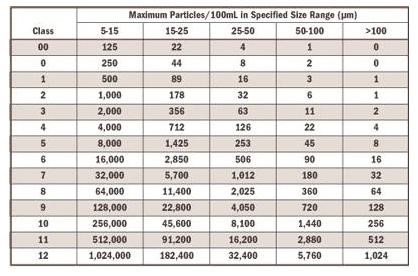
How Particle count affects the oil Systems
Particle count is an important measure of the cleanliness of an oil system, and high particle counts can have negative impacts on the system’s performance and reliability.
When solid particles are present in the oil, they can cause abrasive wear on moving parts, such as bearings, gears, and hydraulic valves. This can lead to increased friction and heat generation, which can further degrade the oil and reduce its lubrication properties. Over time, this can result in increased wear, reduced efficiency, and eventually, equipment failure.
High particle counts can also lead to increased formation of deposits and sludge in the system, which can clog filters, restrict flow, and reduce the effectiveness of other components, such as heat exchangers and cooling systems. This can further exacerbate wear and other issues in the system, leading to decreased performance and reliability.
Regular monitoring of particle count in the oil system can help identify potential issues before they become more serious problems. By tracking changes in particle count over time, maintenance personnel can assess the condition of the oil and take appropriate actions to maintain or improve system performance, such as changing filters, adding oil additives, or flushing and replacing the oil.