Moisture analysis by Karl fisher
Karl Fisher Titration is a technique for the determination of moisture content. The technique was developed by a chemist named Karl Fischer. It is based on a reagent which reacts with water and converts the water into a non-conductive chemical. Karl Fisher provides for the specific detection of water content in a product.
Principle of coulometric KF determinations
The coulometric Karl Fischer titration is a version of the classical water determination method developed by Karl Fischer. The traditional method utilizes a methanolic solution of iodine, sulphur dioxide and a base as buffer. Several reactions run in the titration of a water-containing sample and can be summarized by the following overall equation:
H2O + I2 + [RNH]SO3CH3 + 2 RN ⇔ [RNH]SO4CH3 + 2 [RNH]I
According to the above equation, I2 reacts quantitatively with H2O. This chemical relation forms the basis of the water determination.
In the coulometric Karl Fischer titration, the iodine needed is generated directly in the electrolyte by electrochemical means (“electronic buret”). The rigorously quantitative relationship between
the electric charge and the amount of iodine generated is used for high-precision dispensing of the iodine. As the coulometric Karl Fischer method is an absolute determination no titer need be
Determined. It is necessary only to ensure that the reaction which generates the iodine runs with 100% current efficiency. With the reagents available today this is always the case.
The end point is indicated voltametrically by applying an alternating current of constant strength to a double Pt electrode. This results in a voltage difference between the Pt wires of the indicator electrode which is drastically lowered in the presence of minimal quantities of free iodine. This fact is used to determine the end point of the titration.
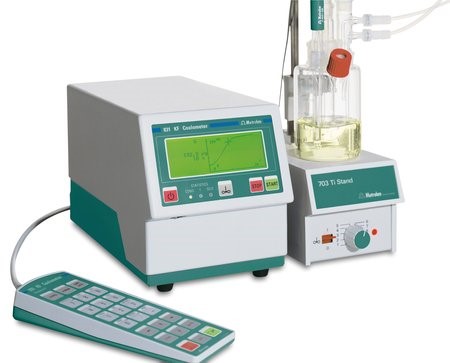
Moisture Determination Procedure
1. The titration vessel has been prepared and the Coulometer is switched on. In the display appears
Press the <START> key.
2. Pre-conditioning begins, i.e. the titration vessel is dried. The “COND” LED blinks. The arrow in the drift display shows the drift tendency (falling, rising, stable).
KFC: wait
Drift: ⇓ 53 ug/min
3. When the titration vessel is dry an acoustic signal is heard and the “COND” LED shows a steady light.
KFC: ready
Drift: ⇔ 4.3 ug/min
4. Press <START> and inject the first sample.
5. Enter the sample size and confirm it with <ENTER>.
Sample size 1.0 g
6. During the titration you will see the curve μg H2O against time. To the left of the curve the following measurements are displayed:
H2O in μg
Rate in μg/min
Time in s
7. After the titration the result is displayed and the titration vessel is continuously kept dry
And the current drift is displayed.
KFC: ready
Drift :⇔ 5.3 ug/min
Content: 38.5 ppm
8. If you want to determine further samples press <START> again and inject the next sample…
Sample size
The sample size should be small so that as many samples as possible can be titrated in the same electrolyte solution and the titration time kept short. However, take care that the sample contains at least 50 μg H2O. The following table provides guidelines for the sample weight.
Content of sample | Sample weight | H2O to be determined |
100000 ppm = 10 % | 50 mg | 5000 μg |
10000 ppm = 1 % | 10 mg… 100 mg | 100 μg…1000 μg |
1000 ppm = 0.1 % | 100 mg… 1 g | 100 μg…1000 μg |
100 ppm = 0.01 % | 1 g | 100 μg |
10 ppm = 0.001 % | 5 g | 50 μg |
Crackle Test for Minerals oil
There are a number of ways to measure the presence of water in oil. However, most of them are complicated, expensive or difficult to use in the field because they employ wet chemistry. One easy way of detecting the presence of free and emulsified water in oil is with the hot-plate crackle test. This simple, tried-and-true method alerts the user to the presence of any free water.
we are screen sample based on visible moisture in oil sample, if we see visible moisture then we first do the crackle test, this help in saving of KF coulometer reagent exhausting as fast as, Crackle test is carried out Under carefully controlled lab conditions, the crackle test is sensitive to around 300-500 ppm (0.03-0.05 percent) of water-in-oil depending on the type of oil.
In this application, the crackle test has been used as a reliable indicator of free and emulsified water. However, with practice and keen eyes and ears, the procedure can be advanced considerably and made more quantitative.
Rather than simply listening for the crackle (scintillation), adding a visual observation and rating of the number and size of the vapor bubbles produced allows a rough indication of the amount of moisture present to be obtained.
The revised method is referred to as the visual crackle. Success in using the procedure depends on practice with varying moisture concentrations in different common fluids, and maintaining a constant hot-plate temperature around 320°F (160°C). A laboratory syringe and a paint shaker can help create a more homogenous suspension, resulting in more consistent results.
Equipment Required
The crackle test can be performed with a minimum of investment using the following equipment:
- Hot plate capable of achieving and maintaining 320°F (160°C) surface temperature.
- Paint shaker (or equivalent) for oil agitation.
- Oil dropper tube or lab syringe.
Procedure
- Raise the hot plate temperature to 320°F (160°C). Always use the same temperature.
- Violently agitate oil sample to achieve homogenous suspension of water in oil.
Using a clean dropper, place a drop of oil on the hot plate.
Observations
- If no crackling or vapor bubbles are produced after a few seconds, no free or emulsified water is present.
- If very small bubbles (0.5 mm) or listen sound of 2-3 crackle are produced but disappear quickly, approximately 0.03 to 0.06 percent water is present.
- If bubbles approximately 2 mm are produced, gather to the center of the oil spot, enlarge to about 4 mm, then disappear, approximately 0.7 to 0.2 percent water is present.
- For moisture levels above 0.2 percent, bubbles may start out about 2 to 3 mm then grow to 4 mm, with the process repeating once or twice. For even higher moisture levels, violent bubbling and audible crackling may result.
Limitations
Although generally applicable, the crackle test does have some limitations:
- The method is nonquantitative.
- Hot plate temperatures above 320°F (160°C) induce rapid scintillation that may be undetectable.
- The method does not measure the presence of chemically dissolved water.