What is Oil Testing ?
Oil testing or Oil analysis is the process of analyzing the physical, chemical, and performance characteristics of different types of oils, such as crude oil, refined petroleum products, lubricants, and edible oils. The purpose of oil testing is to ensure that the oils meet the required safety, environmental, and performance standards for their intended use. This involves a range of tests, including measuring the viscosity, density, flash point, color, and chemical composition of the oil, as well as evaluating its ability to perform its intended function, such as reducing friction, preventing wear and tear, and withstanding high temperatures. Oil testing is crucial in various industries, including oil and gas, automotive, aviation, and food processing, to maintain the quality, safety, and integrity of the oils used in these industries.
Importance of Oil Testing
Oil analysis is a routine activity for analyzing oil health, oil contamination and machine wear. The purpose of an oil analysis program is to verify that a lubricated machine is operating according to expectations. When an abnormal condition or parameter is identified through oil analysis, immediate actions can be taken to correct the root cause or to mitigate a developing failure.
Why we perform oil analysis
An obvious reason to perform oil analysis is to understand the condition of the oil, but it is also intended to help bring to light the condition of the machine from which the oil sample was taken. There are three main categories of oil analysis: fluid properties, contamination and wear debris.
Fluid Properties
This type of oil analysis focuses on identifying the oil’s current physical and chemical state as well as on defining its remaining useful life (RUL). It answers questions such as:
- Does the sample match the specified oil identification?
- Is it the correct oil to use?
- Are the right additives active?
- Have additives depleted?
- Has the viscosity shifted from the expected viscosity? If so, why?
- What is the oil’s RUL?
Contamination
By detecting the presence of destructive contaminants and narrowing down their probable sources (internal or external), oil analysis can help answer questions such as:
- Is the oil clean?
- What types of contaminants are in the oil?
- Where are contaminants originating?
- Are there signs of other types of lubricants?
- Is there any sign of internal leakage?
Wear Debris
This form of oil analysis is about determining the presence and identification of particles produced as a result of mechanical wear, corrosion or other machine surface degradation. It answers questions relating to wear, including:
- Is the machine degrading abnormally?
- Is wear debris produced?
- From which internal component is the wear likely originating?
- What is the wear mode and cause?
- How severe is the wear condition?
You need to know if any actions should be taken to keep the machine healthy and to extend the life of the oil. Oil analysis for machines can be compared to blood analysis for the human body. When a doctor pulls a blood sample, he puts it through a lineup of analysis machines, studies the results and reports his conclusions based on his education, research and detailed questions asked to the patient.
Likewise, with oil analysis, careful oil samples are taken, and elaborate machines yield the test results. Laboratory personnel interpret the data to the best of their ability, but without crucial details about the machine, a diagnosis or prognosis can be inaccurate. Some of these important details include:
- The machine’s environmental conditions (extreme temperatures, high humidity, high vibration, etc.)
- The originating component (steam turbine, pump, etc.), make, model and oil type currently in use
- The permanent component ID and exact sample port location
- Proper sampling procedures to confirm a consistently representative sample
- Occurrences of oil changes or makeup oil added, as well as the quantity of makeup oil since the last oil change
- Whether filter carts have been in use between oil samples
- Total operating time on the sampled component since it was purchased or overhauled
- Total runtime on the oil since the last change
- Any other unusual or noteworthy activity involving the machine that could influence changes to the lubricant
Interpreting an oil analysis report can be overwhelming to the untrained eye. Oil analysis isn’t cheap, and neither is the equipment on which it reveals information. Every year, industrial plants pay millions of dollars for commercial laboratories to perform analysis on used and new oil samples. Unfortunately, a majority of the plant personnel who receive these lab reports do not understand the basics of how to interpret them.
What to Look for When Reviewing an Oil Analysis Report
- Read and check the data on the oil type and machine type for accuracy.
- Verify that reference data is shown for new oil conditions and that trend data is at an understood frequency (preferably consistent).
- Check the measured viscosity.
- Verify elemental wear data and compare to reference and trended data. Use a wear debris atlas to match elements to their possible source.
- Check the elemental additive data and compare to reference and trended data. Use a wear debris atlas to match elements to their possible source.
- Verify elemental contamination data along with particle counts and compare with reference and trended data. Use a wear debris atlas to match elements to their possible source.
- Check moisture/water levels and compare to reference and trended data.
- Verify the acid number and base number and compare to reference and trended data.
- Check other analyzed data such as FTIR oxidation levels, flash point, demulsibility, analytical ferrography, etc.
- Compare any groups of data that are trending toward unacceptable levels and make justifications based on these trends.
- Compare written results and recommendations with known information on the oil and machine, such as recent changes in environmental or operational conditions or recent oil changes/filtration.
- Review alarm limits and make adjustments based on the new information.
Typically, an oil analysis report comes with a written summary section that attempts to put the results and recommendations in layman’s terms. But, since the laboratory has never seen the machine or know its full history, these recommended actions are generic and not tailored to your individual circumstances. Therefore, it is the responsibility of the plant personnel who receive the lab report to take the proper action based on all known facts about the machine, the environment and recent lubrication tasks performed.
Oil Analysis Tests
For a standard piece of equipment undergoing the normal recommended oil analysis, the test slate would consist of “routine” tests. If more testing is needed to answer advanced questions, these would be considered “exception” tests.
Routine tests vary based on the originating component and environmental conditions but should almost always include tests for viscosity, elemental (spectrometric) analysis, moisture levels, particle counts, Fourier transform infrared (FTIR) spectroscopy and acid number. Other tests that are based on the originating equipment include analytical ferrography, ferrous density, demulsibility and base number testing.
The table on the left shows how tests are used in each of the three main oil analysis categories.
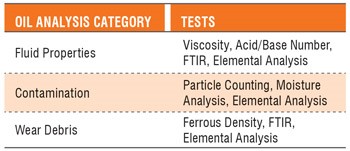
Viscosity
Several methods are used to measure viscosity, which is reported in terms of kinematic or absolute viscosity.
Kinematic Viscosity
Kinematic viscosity is a measure of a fluid’s internal resistance to flow under gravitational forces. It is determined by measuring the time in seconds, required for a fixed volume of fluid to flow a known distance by gravity through a capillary within a calibrated viscometer at a closely controlled temperature.
This value is converted to standard units such as centistokes (cSt) or square millimeters per second. Viscosity reporting is only valid when the temperature at which the test was conducted also is reported – for example 23 cSt at 40 degrees C.
Several engineering units are used to express viscosity, but the most common by far are centistoke (cSt) for kinematic viscosity and the centipoise (cP) for dynamic (absolute) viscosity.
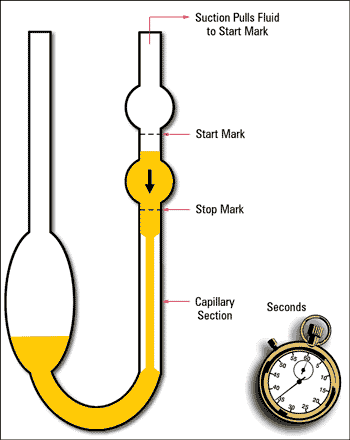
Measuring Dynamic Viscosity (Absolute Viscosity)
Dynamic viscosity is measured as the resistance to flow when an external and controlled force (pump, pressurized air, etc.) forces oil through a capillary (ASTM D4624), or a body is forced through the fluid by an external and controlled force such as a spindle driven by a motor. In either case, the resistance to flow (or shear) as a function of the input force is measured, which reflects the internal resistance of the sample to the applied force, or its dynamic viscosity.
Acid Number/Base Number
Acid number and base number tests are similar but are used to interpret different lubricant and contaminant-related questions. In an oil analysis test, the acid number is the concentration of acid in the oil, while the base number is the reserve of alkalinity in the oil. Results are expressed in terms of the volume of potassium hydroxide in milligrams required to neutralize the acids in one gram of oil. Acid number testing is performed on non-crankcase oils, while base number testing is for over-based crankcase oils.
An acid number that is too high or too low may be the result of oil oxidation, the presence of an incorrect lubricant or additive depletion. A base number that is too low can indicate high engine blow-by conditions (fuel, soot, etc.), the presence of an incorrect lubricant, internal leakage contamination (glycol) or oil oxidation from extended oil drain intervals and/or extreme heat.
FTIR (Fourier-transform infrared spectroscopy)
FTIR is a quick and sophisticated method for determining several oil parameters including contamination from fuel, water, glycol and soot; oil degradation products like oxides, nitrates and sulfates; as well as the presence of additives such as zinc dialkyldithiophosphate (ZDDP) and phenols.
The FTIR instrument recognizes each of these characteristics by monitoring the shift in infrared absorbance at specific or a range of wavenumbers. Many of the observed parameters may not be conclusive, so often these results are coupled with other tests and used more as supporting evidence. Parameters identified by shifts in specific wavenumbers are shown in the table below.
Elemental Analysis of oil
Elemental analysis works on the principles of atomic emission spectroscopy (AES), which is sometimes called wear metal analysis. This technology detects the concentration of wear metals, contaminants or additive elements within the oil. The two most common types of atomic emission spectroscopy are rotating disc electrode (RDE) and inductively coupled plasma (ICP).
Both of these methods have limitations in analyzing particle sizes, with RDE limited to particles less than 8 to 10 microns and ICP limited to particles less than 3 microns. Still, they are useful for providing trend data. Possible sources of many common elements are shown in the table below.
The best way to monitor this type of data is to first determine what is expected to be in the oil. An effective oil analysis report will provide reference data for the new oil so any amounts of additive elements can be easily distinguished from those of contaminants. Also, because many types of elements should be expected at some level (even contaminants in certain environments), it is better to analyze trends rather than focus on any specific measurement of elemental analysis data.
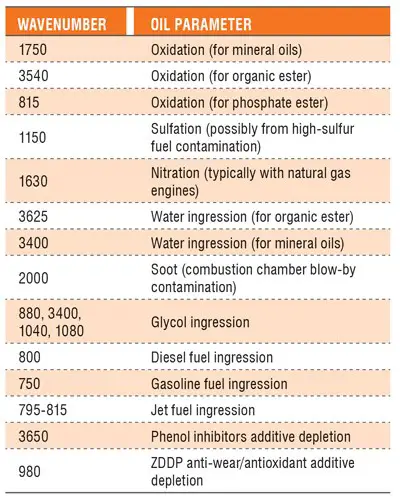
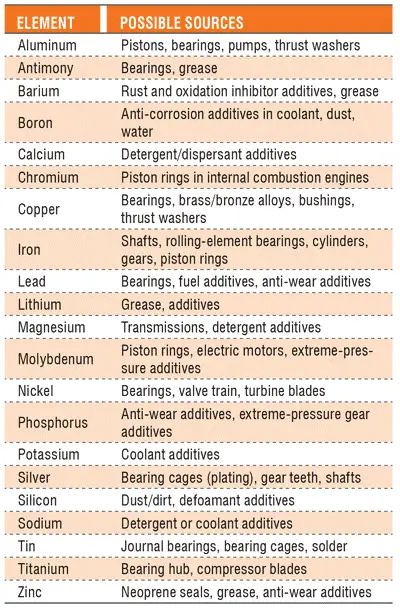
NAS Analysis (Particle Count)
The National Aerospace Standard (NAS) 1638 was developed in the 1960s to help control the contamination levels of hydraulic fluid within hydraulic components. NAS 1638 became a standard not only for the aerospace industry but also throughout many other industries as well. The latest version of NAS 1638 is SAE 4059.
Nevertheless, in many areas of industry, NAS 1638 has largely been outpaced by the ISO 4406 standard in recent years. Both NAS 1638 and ISO 4406 focus on the methods for calculating particle counts or solid contamination levels within a fluid.
NAS 1638 represents the counts of particles in five size groups:
- 5 to 15 microns per 100 milliliters (mL)
- 15 to 25 microns per 100 mL
- 25 to 50 microns per 100 mL
- 50 to 100 microns per 100 mL
- >100 microns per 100 mL
ISO 4406:1999 represents the counts of particles in three size groups:
- >4 microns per 1 mL
- >6 microns per 1 mL
- >14 microns per 1 mL
From these five groups of particle sizes and a basic particle size distribution, NAS 1638 reports the results in 14 distinct classes of particle counts numbered 00, 0 and 1 through 12, with 00 being the cleanest and 12 being the dirtiest. Each proceeding class contains twice the number of particles as the previous class per each of the five particle size groups (see the table below).
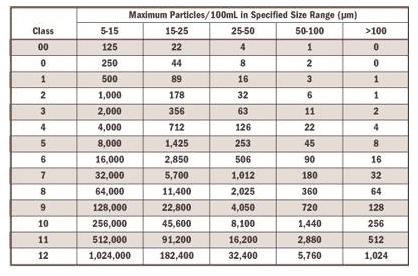
Moisture Analysis
Moisture content within an oil sample is often measured with the Karl Fischer titration test. This test reports results in parts per million (ppm), although data is often shown in percentages. It can find water in all three forms: dissolved, emulsified and free. The crackle test and hot-plate test are non-instrument moisture tests for screening before the Karl Fischer method is used. Possible reasons for a moisture reading being too high or too low would include water ingression from open hatches or breathers, internal condensation during temperature swings or seal leaks.
Flash point
The lowest temperature at which a liquid (usually a petroleum product) will form a vapour in the air near its surface that will “flash,” or briefly ignite, on exposure to an open flame. The flash point is a general indication of the flammability or combustibility of a liquid. Below the flash point, insufficient vapour is available to support combustion.
Fire Point
The temperature above the flash point, the liquid will produce enough vapour to support combustion known as fore point.
Pour Point
It is defined as the minimum temperature in which the oil has the ability to pour down from a beaker. In crude oil a high pour point is generally associated with a high paraffin content, typically found in crude deriving from a larger proportion of plant material.
Nice post sir
Very nice post sir